一、MOM的演进与定义
MOM(Manufacturing Operations Management)概念起源于2000年ISA-95标准,该标准首次明确了制造运营管理的边界与模型24。相较于早期MES系统聚焦车间生产执行,MOM扩展了管理维度:
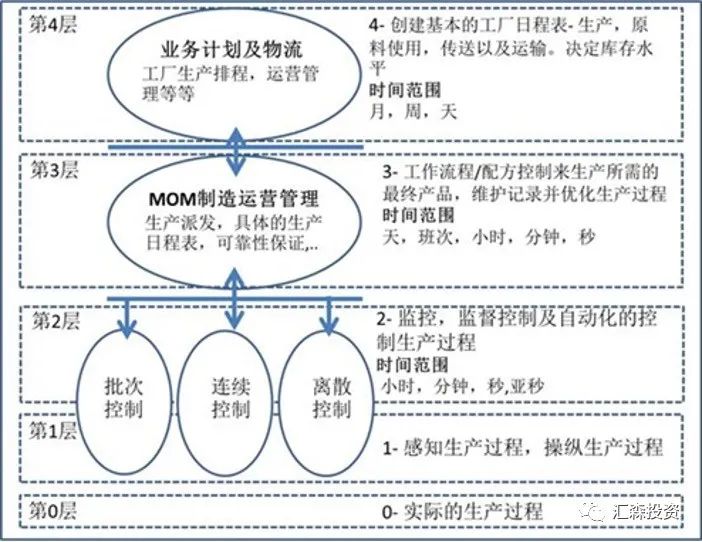
四、系统实施关键要素
- 需求精准定位:依据ISA-95标准构建四级功能模型(业务计划-制造运营-过程控制-设备控制),明确各层级数据交互规范28;
- 技术路线选择:混合采用低代码平台(快速构建基础模块)与定制开发(处理复杂业务逻辑),平衡实施周期与功能适配性311;
- 组织管理:建立跨部门协同机制,如某电子企业通过设立MOM卓越中心,推动200+业务流程标准化59;
- 安全体系构建:采用零信任架构,对OT数据实施端到端加密,确保生产数据泄露风险降低至0.01%以下59。
随着数字孪生、工业元等新技术融合,MOM系统正从生产管理工具进化为企业数字化的心中枢。西门子Oenter、IMS-MOM等平台已实现与边缘计算设备的深度集成,支持毫秒级数据采集与自主决策79。未来制造企业的竞争力,将取决于其MOM系统对资源优化配置的深度与市场变化的敏捷度。
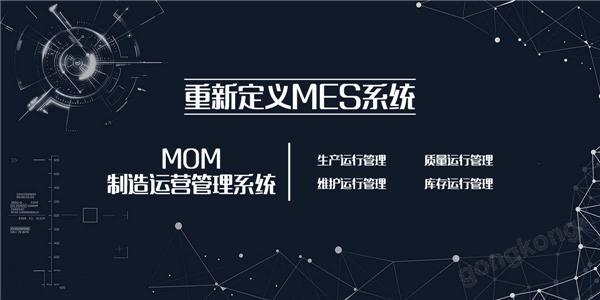
- 多维集成能力:采用RESTful API实现与ERP、PLM、WMS等系统的无缝对接712;
- 智能分析引擎:内置机器学习算,可对生产瓶颈进行根因分析并生成优化建议39;
- 可视化界面:通过3D数字孪生技术呈现车间实时状态,异常速度提升60%79。
三、行业应用值体现
在汽车制造领域,特斯拉通过MOM系统实现工厂生产计划协同,订单交付周期缩短至7天以内35;半导体行业应用中,某芯片企业借助MOM的质量追溯模块,将产品缺陷率从500PPM降至80PPM79;在航空制造业,波音采用MOM维护管理功能,发动机大修间隔周期延长至12,000飞行小时57。
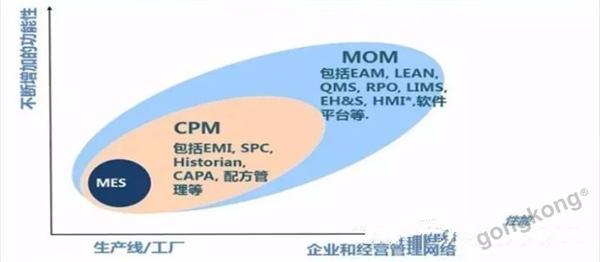
- 管理范围延伸:从单一生产执行拓展至生产运行、维护运行、质量运行、库存运行四大心领域,形成全流程闭环管理110;
- 数据整合升级:聚合SCADA、PLC等自动化系统数据,结合人工录入信息,构建覆盖工厂及供应链的实时数据23;
- 工业4.0适配:通过物联网、边缘计算等技术满足智能制造对实时、预测性决策的需求79。
二、功能架构与技术特性
典型MOM系统包含五大心模块及三大技术特征:
心功能模块:
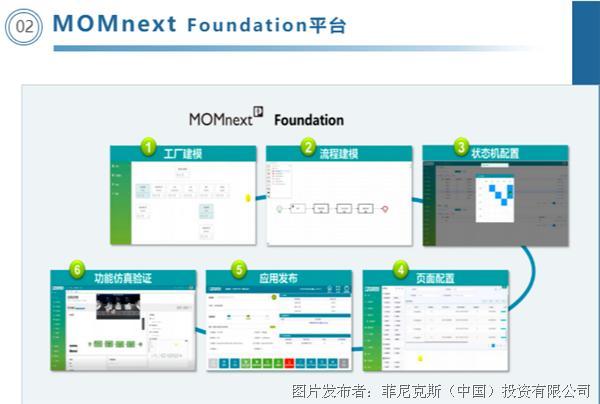
从财务视角看,MOM实施可带来显著效益:某装备制造企业引入系统后,直接生产成本降低12%,设备综合效率(OEE)提升18%,同时获得授信额度增加30%59。
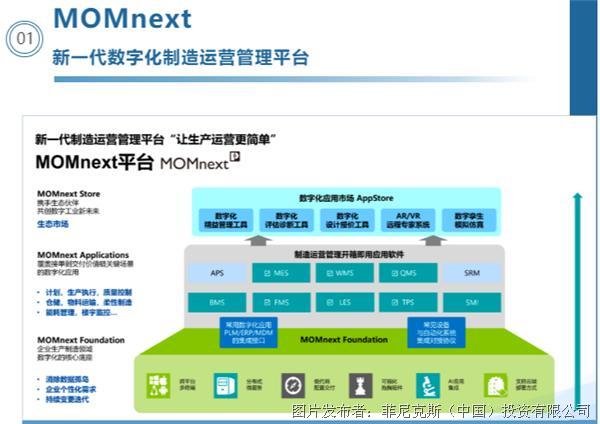
- 生产管理:支持多工厂协同排产,通过APS算优化生产计划,实现工单执行进度实时追踪312;
- 质量管理:集成SPC统计过程控制,支持缺陷自动检测与根源追溯,降低质量成本约15%-20%17;
- 设备管理:运用预测性维护技术,结合设备OEE分析,减少非计划停机时间30%以上37;
- 库存管理:通过RFID/条码技术实现物料全生周期追踪,库存周转率提升可达25%35;
- 能源管理:监测水电气消耗,支撑碳足迹算,助力企业达成ESG目标59。
技术架构特征:
MOM制造运营是制造执行系统(MES)的演进形态,其心在于通过数字化技术整合生产全流程资源,实现制造过程的精细化、透明化与智能化管理。以下从概念演进、功能架构、应用值及实施要点等维度展开论述。
相关问答